When it comes to compact machine tools, the DNM 4000 machining center by DN Solutions has been making waves. Its reputation is built on a blend of power, precision, and a thoughtful design that maximizes productivity without taking up excessive floor space. In this article, we'll delve into the world of the DNM 4000 cnc machining center, uncovering its features, advantages, and how it aligns with the modern needs of manufacturers.
Compact Yet Powerful
Floor space is a precious commodity in modern manufacturing facilities and machine shops, where every square foot is scrutinized for its potential to impact efficiency and productivity. The DNM 4000, a cutting edge milling machine, understands this challenge and addresses it head-on with its compact footprint.
At first glance, the DNM 4000 machining center might appear unassuming in its size, but beneath its modest exterior lies a formidable machining center. This compact powerhouse is engineered for excellence, leveraging its compact design to optimize floor space without sacrificing performance. In today's fast-paced manufacturing landscape, where every inch of the shop floor matters, the DNM 4000's footprint is a strategic advantage.
The heart of the DNM 4000's power is its directly-coupled 40 taper spindle. This spindle is the driving force behind its exceptional performance. Unlike traditional belt-driven spindles, the direct-coupled spindle minimizes vibration and noise during high-speed operations. The reduction in vibration not only enhances machining precision but also contributes to a more comfortable and eco-friendly working environment.
By choosing a directly-coupled spindle, DN Solutions Machine Tools has demonstrated its commitment to both performance and sustainability. This innovative design not only boosts machine performance but also aligns with modern expectations for environmentally responsible manufacturing. The DNM 4000 proves that you can have power, precision, and environmental consciousness in one compact package.
Operator-Friendly Design
In the world of machining, the role of the operator is pivotal. Their efficiency and convenience directly impact the productivity of the entire machining process. Recognizing this, the DNM 4000 machining center has been meticulously designed with the operator's needs in mind.
One of the standout features of the DNM 4000 vertical machining center is its operator-friendly design, epitomized by the inclusion of two doors. These doors provide easy access for operators, ensuring swift and efficient setup and maintenance. In a high-demand machining environment, where time is often the most precious resource, quick access to the machine is invaluable.
But the operator-friendly design of the DNM 4000 machining center goes beyond easy access. It extends to features like effective bed flushing for chip removal. This might sound like a small detail, but in practice, it's a game-changer.
Efficient chip removal is essential in maintaining uninterrupted machining operations. By minimizing the time spent on chip-related issues, the DNM 4000 keeps downtime to a minimum and productivity at its peak.
Vibration-Free Performance
Vibration and noise are often unwanted companions in machine tool centers, causing disruptions and affecting the quality of the final product. The DNM 4000 addresses this concern with its directly-coupled spindle.
By reducing vibration and noise during high-speed operations, this machine ensures a stable and pleasant working environment. Operators can work efficiently without the distraction of excessive noise, while the machine quietly delivers precision results.
Precision and Convenience
When it comes to machine tools, precision is paramount. To achieve this, the DNM 4000 comes equipped with a standard thermal error compensation function. This function accounts for thermal changes during machining, ensuring that precision is maintained throughout the entire process.
Additionally, the machine features the Easy Operation (Ez work) function, designed to make machine operation as convenient as possible. This combination of precision and user-friendliness sets the DNM 4000 apart in the world of machining.
Cost-Effective Lubrication
Maintenance costs and machine uptime are of utmost importance in any machining operation. The DNM 4000 adopts a grease lubrication system for its roller guideways. This innovative choice not only offers a cleaner solution but also reduces annual maintenance costs by a substantial 55%.
With greasing required only once every three months, the need for frequent oiling is eliminated. Furthermore, the absence of slideway oil in the coolant prevents the need for an oil skimmer, contributing to a more pleasant working environment by eliminating unpleasant odors.
Cutting Performance and CNC Compatibility
Ultimately, the true test of any machining center lies in its cutting performance. The DNM 4000, with its #40 spindle, excels in this regard. It boasts travel distances of 520 mm (X-axis), 400 mm (Y-axis), and 480 mm (Z-axis), providing ample room for precision work. Furthermore, it supports various CNC systems, including DN Solutions FANUC i and SIEMENS, offering versatility for different machining requirements.
In the ever-evolving world of machining, the DNM 4000 stands as a testament to the marriage of power and efficiency. Its compact design, operator-friendly features, reduced vibration, and cost-effective lubrication system make it a worthy addition to any manufacturing facility.
As modern manufacturing needs continue to demand efficiency, precision, and reliability, the DNM 4000 vertical machining center shines as a versatile solution. When every second and every micron matter, this machine proves itself as a valuable asset in the quest for machining excellence. If you’re interested to learn more about it, contact us now at Machine Tool Specialties.
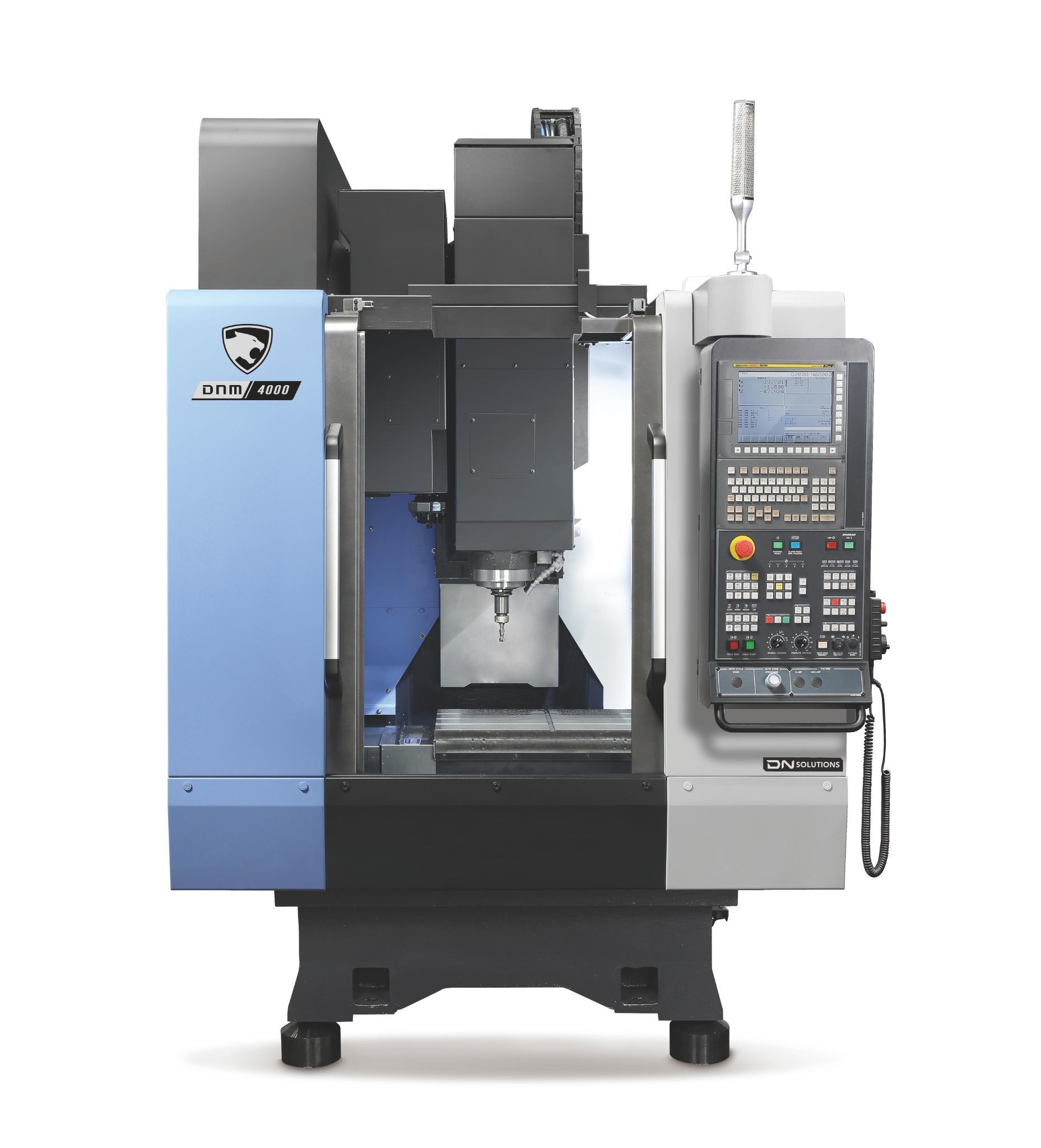